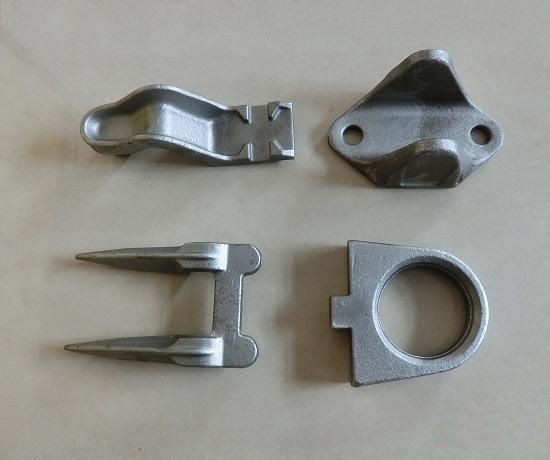
Warm forging is performed with the workpiece heated to a range that is generally above the work hardening temperature and below the temperature at which scale forms. The process fills the niche between the closer tolerance, but sometimes expensive cold forging process and the somewhat lower precision hot forging process. It is being used to produce close tolerance components in steel alloys that were not feasible or impossible by cold forging. It is also being used to produce components very […]
Tags: Warm Forging