Injection molding is a manufacturing process used to produce single parts and products using various materials, most commonly thermosetting and thermoplastic polymers.
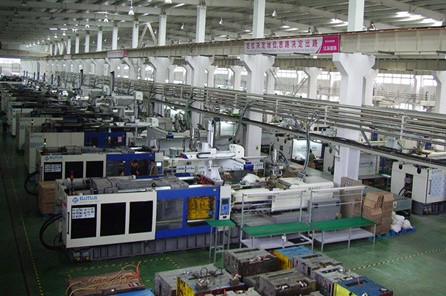
Injection molding machines in a large factory
Today, injection molding is the most popular method of manufacturing parts and is used to produce a variety of everyday plastic products, including packaging, toys, telephones, bottle lids, chairs and many more. Injection molding is also used to manufacture complex, small metal parts, known as Metal Injection Molding (MIM). But just how does injection molding work?
The machine
An injection molding machine consists of a material hopper, a plunger and a heating barrel. The machine works to exert pressure and secure the mould in place during the injection process, and the type of machine that is used will be determined by the type of part being molded and the material being used. For example, large parts and stiff materials will require machines that can exert a high clamping force and powerful injection pressure.
The process
Once the part for the product has been designed, the metal mould is precision-machined to create the desired shape, either as a single cavity or multiple cavities. The chosen material for the part, usually taking the form of plastic granules, is fed through a heated chamber and forced through a plunger into a hollow mould. After the cavity has been filled, the machine exerts pressure to ensure that the plastic does not collapse. The part then cools, solidifies and is ejected from the mould.
As well as the aforementioned process, there are various other injection molding procedures, including metal injection molding, die casting, thin-wall injection molding and silicone rubber injection molding.
Materials
To determine what type of material is used for the part, the particular function of the final product needs to be taken into consideration.
However, thermoplastics is usually the preferred material for injection molding, mainly due to their desirable properties. Thermoplastics are recyclable, extremely versatile and will easily soften when heated. Thermosets and elastomers can also be used for injection molding, although they are not as widely used.
Whilst the majority of moulds are constructed from steel, other metals including stainless steel, copper alloy and aluminium can also be used for specific procedures. Aluminium for example, is ideal for low volume production and large parts, but is unsuitable for high volume applications as it can be susceptible to damage.
Benefits
There are a number of reasons as to why injection molding is one of the most popular modern manufacturing techniques. Firstly, the procedure is quick and efficient, making it ideal for manufacturers to produce large amounts of identical objects with extreme precision and accuracy. Whilst the initial cost of injection molding may be high, the ability for mass production is extremely cost-efficient way to manufacture goods.
Additionally, the shape of the mould can be as simple, or as complicated, as the design requires, from small components to entire car body panels.
Tags: Injection Molding